With iFIX and WorkFlow, Sirca increases the quality and safety of its resin production and lays the foundations for continuous process improvement.
From car tanks to boat chassis, up to artificial marble floors: unsaturated polyester resins are a product that is widely used in the composite materials sector.
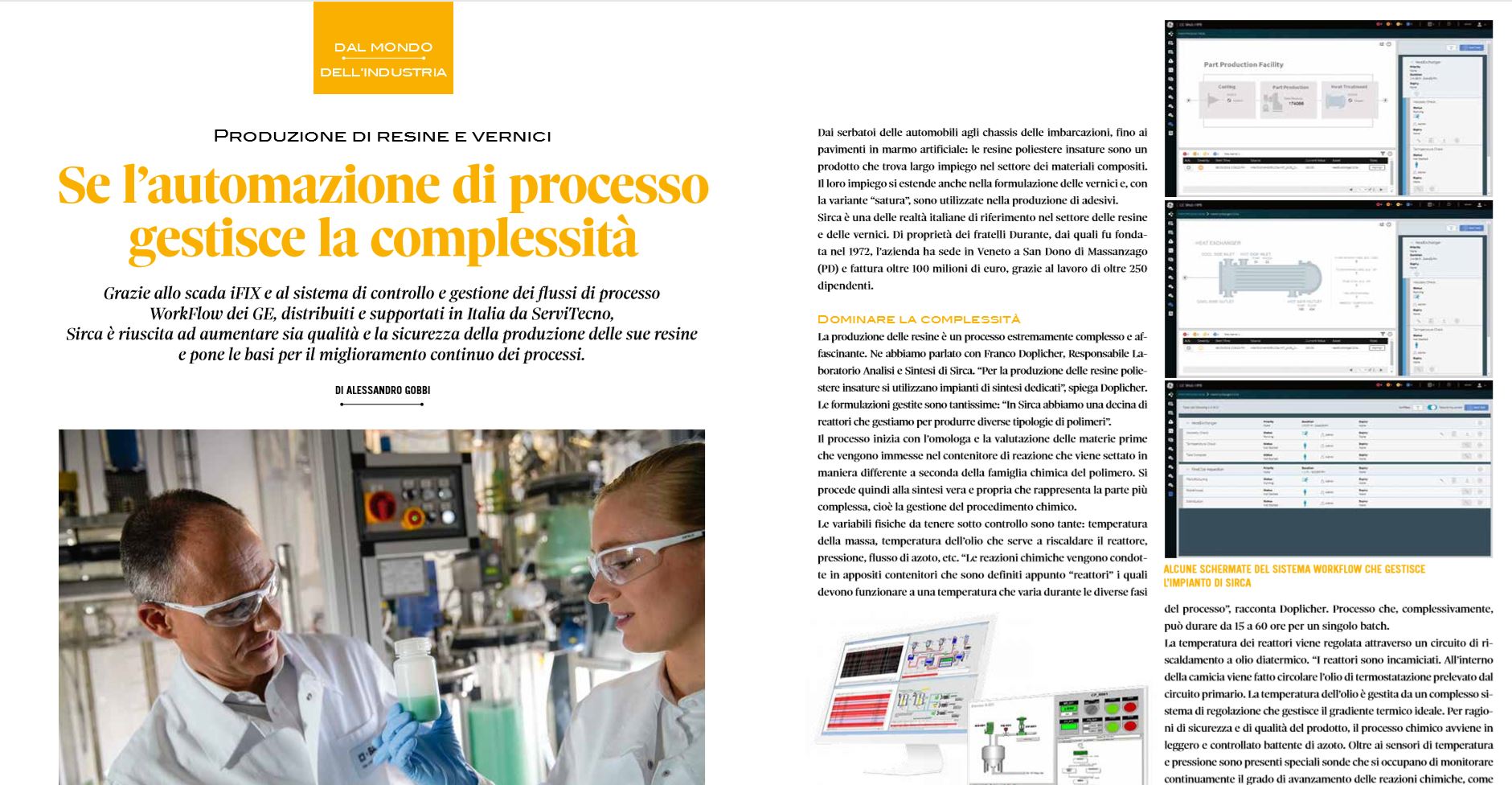
Sirca Case History – download the original article
Their use also extends to the formulation of paints and, with the "saturated" variant, they are used in the production of adhesives.
Sirca is one of the Italian companies of reference in the resin and paint sector. Owned by the Durante brothers, who founded it in 1972, the company is based in the Veneto region at San Dono di Massanzago (PD) and has a turnover of over 100 million euros, thanks to the work of over 250 employees.
Dominate the complexity
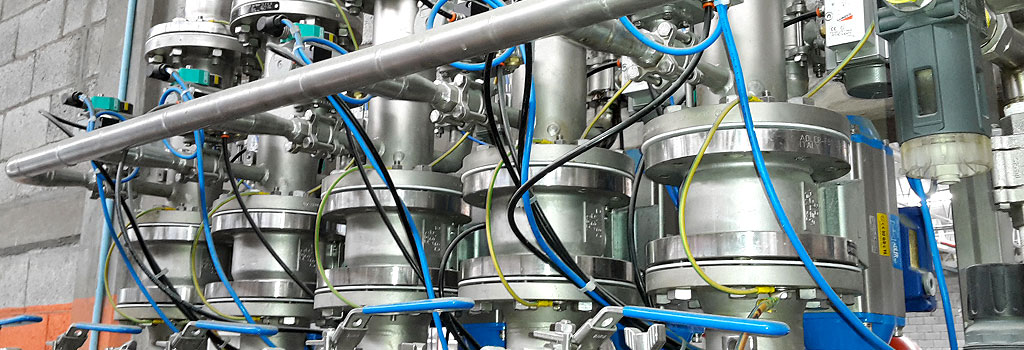
The production of resins is an extremely complex and fascinating process.
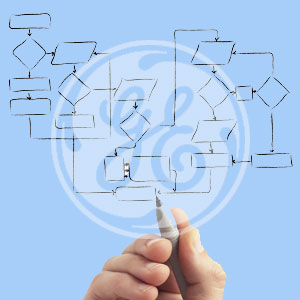
We talked about it with Franco Doplicar, Head of Analysis and Synthesis Laboratory of Sirca.
"Dedicated synthesis plants are used for the production of unsaturated polyester resins“, explains Doplicher. The managed formulations are many: “In Sirca we have about ten reactors that we manage to produce different types of polymers".
The process begins with the approval and evaluation of the raw materials which are introduced into the reaction container which is set up differently according to the chemical family of the polymer.
We then proceed to the actual synthesis which represents the most complex part, i.e. the management of the chemical process.
There are many physical variables to keep under control: temperature of the mass, temperature of the oil used to heat the reactor, pressure, nitrogen flow, etc.
"The chemical reactions are carried out in special containers which are precisely defined as "reactors" which must operate at a temperature which varies during the various stages of the process“, says Doplicher.
Process which, overall, can last from 15 to 60 hours for a single batch. The temperature of the reactors is regulated through a diathermic oil heating circuit.
"The reactors are jacketed. The temperature control oil taken from the primary circuit is circulated inside the jacket. The oil temperature is managed by a complex regulation system which manages the ideal thermal gradient. For safety and product quality reasons, the chemical process takes place in a light and controlled nitrogen head. In addition to the temperature and pressure sensors, there are special probes that continuously monitor the progress of chemical reactions, such as spectrophotometers and viscometers. The variables involved are therefore different and the data generated in a process can reach considerable complexity".
Access data to govern the process
Even if sector regulations do not impose traceability obligations, Sirca has long understood the importance of having the data generated in each plant process fraction under control: from the management of the primary oil circuit to that of the oil in the wall, from the temperature of the mass in reaction up to the pressure.
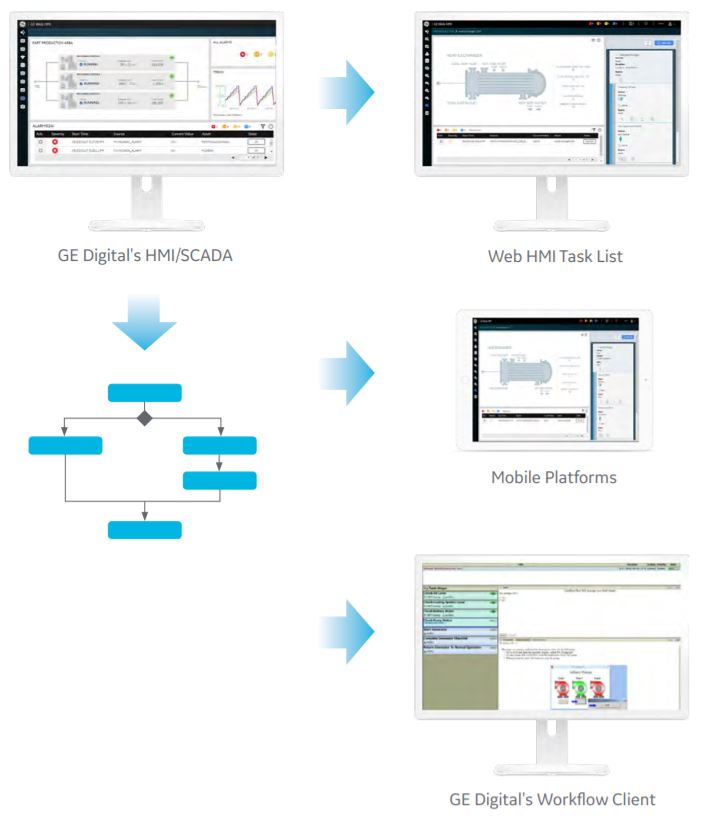
After a few years, the production monitoring and control system used by Sirca had become obsolete, making process data consultation excessively slow."This – explains Doplicher – requires timely and fast data logging. Data logging and analysis are essential for studying, understanding and improving the phases of the chemical process so as to obtain a polymer with a high and constant quality over time while guaranteeing the safety of the chemical process".
This is one of the reasons which, a few years ago, prompted Sirca to rely on GE's scada, iFIX, distributed and supported in Italy by ServiTecno.
For implementation, Sirca relied on a leading company operating throughout the Veneto region and abroad.
The automation branded iFIX
"Our choice was mainly dictated by the need to have a good archiving system. It is crucial for us to have our data always available and accessible quickly. In a batch, whose processing takes 60 hours, a considerable amount of data is generated, both for the number of controlled variables and for the sampling frequency“, says Doplicher.
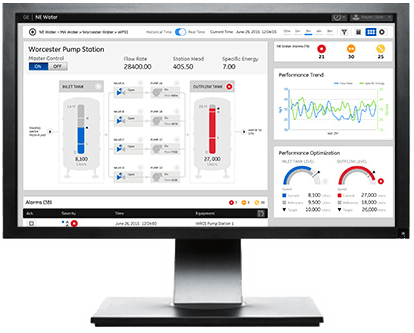
"Extracting data about any point in the process is not an easy task and iFIX has proven it can do it well".
Year after year the implementation of iFIX extension she continued.
Today the system manages about seven thousand variables coming from a dozen PLCs. “The architecture of the platform includes an iFix server, a terminal server to manage the various clients, a Historian server and a WorkFlow server”, explains the system integrator commissioned by Sirca.
All these servers are virtualized on a powerful physical machine taken care of by Sirca's IT department. “Through the terminal server iFIX sends the information to different clients. However, here too it was decided to optimize hardware resources”, underlines the technician. “In the reactor area, for example, there are two PCs with 7 remote desktop connections associated with as many monitors.
From each monitor it is possible, with the necessary authorisations, to see the screens of the whole system”. The domain of iFIX then also extends to the laboratory, the catalyst dosing plant and other areas of production.
Data storage – the critical resource for Sirca – is taken care of by the Historian server, which today manages all the variables. What is the secret of its speed?
"GE Historian uses an advanced data compression technique that allows you to store a large amount of data without taking up much space or slowing down your machine“, explains the system administrator.
Data which, moreover, are extremely simple to consult: a special "view" allows you to access the trends, which load the different groups of variables.
The operator can move over time very simply to trace the status of the variables of a given historical moment. Finally, queries have been prepared that allow you to export values or tables in Excel format.
WorkFlow, the extra man on the team
Last year Sirca also decided to change the process flow control and management system, choosing GE WorkFlow.
It is a system that has a dual task: to directly and automatically manage some adjustments and to process the workflows that will be transmitted to the field personnel.
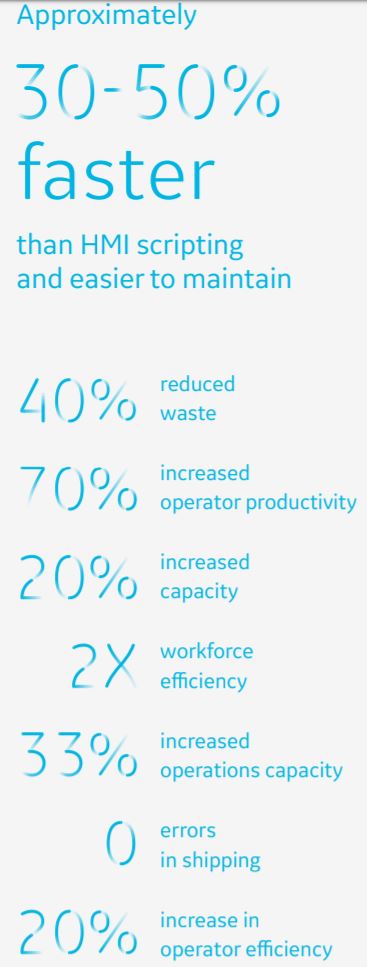
"Having a tool that can continuously perform small process adjustments allows you to significantly improve the quality of the process itself. Let us take the case of regulating a thermal gradient which, for example, must raise the temperature of the reactor by 40 degrees in two hours. An operator would adjust the variable discontinuously with rather wide intervals (25-30 minutes), while with WorkFlow the operation can take place with many more interventions which guarantee precision and gradualness of the increase“, explains Doplicher.
But WorkFlow is also able to generate visual instructions for operators in the field: from a series of information entered in textual format, sets of sequential instructions are generated which tell the operator step by step what interventions to do. “WorkFlow is not only allowing us to eliminate paper instructions, but it is a far better tool than other electronic solutions that work offline: the advantages of having a system that 'lives' with the process are considerable".
Another benefit that WorkFlow offers is simplicity.
"WorkFlow offers an optimized feeling for the viewer of the terminal. But GE hasn't forgotten the work of process developers either. Too often, creating workflows via programs ended up being slow and painful. WorkFlow, on the other hand, has also been designed keeping in mind the needs of the process engineer".
"To win the game of competitiveness you need to work as a team, from the process engineer to the worker who takes care of the more manual tasks. The feeling, however, is that with WorkFlow today the team can count on one more man".
WorkFlow is proving to be better, more versatile and above all better interconnected than the previously used system.
"When an instruction is given, for example, it is possible to connect other instructions written in WorkFlow in parallel. This is a factor of great importance for those who manage complex processes or multiple processes as in our case. For example, the software can deal directly with the thermal increase and in parallel give instructions to the operator on another work area of the reactor“. Over the months, WorkFlow is increasingly gaining Sirca's trust.
"We also recently contracted GE iFIX to manage a line in the paint department. And, if things continue to go well, it is possible that we will decide to use WorkFlow there in the future as well".