Plant Applications 2024 | Coming Soon!
Applications for Proficy, Cloud OEE and Cloud MES systems
Find out why four analyst firms named GE a leader in MES, how we help manufacturers meet sustainability requirements, overcome supply chain disruptions, and converge OT/IT to power digital transformation.
- New enterprise-grade multi-site capabilities and backend modernization for maximum scalability and built-in high availability (SaaS edition)
- Optimize across the enterprise with improved scalability with Kubernetes support for the backend and web client front end for the Cloud (SaaS edition)
- Simplify administration with the web-based Configuration Hub plugin, gain compatibility with the 64-bit Excel Add-In (available now via the Support Community), and capture manual data more efficiently with a new Autolog.
- Accelerate time to value: Faster issue resolution with integrated Elastic Search, downtime widgets, and operator to-do list widgets for Operations Hub
- Improve discrete manufacturing with new out-of-the-box capabilities: Engineering Change Order to ensure accurate and approved changes to new and ongoing work orders, operator qualifications on operations, tool tracking during job execution order, NCM extensions, ability to define downgraded material and more.
- Reduce downtime with new predictive analytics capabilities: Predictive Downtime and True Root Cause Downtime
Why are we talking about 1%?
“1% is a remarkable percentage when it comes to savings, in any business: thanks to the module Efficiency of Plant Application it is possible to improve in every sector, producing more, better and with lower costs”.
The machines cannot always work continuously or at maximum speed as they undergo various stops and could produce defective parts. In order for a machine (or a line) to meet its performance and quality standards, it is essential that it continues to produce or deliver a service without problems of downtime or incorrect reproduction of the product.
These problems are the direct cause of the reduction in machine efficiency as measured by the OEE: there are 3 macro categories into which we can divide system problems, and none of these must be underestimated.
The main elements used to calculate the OEE are therefore:
- Availability: losses due to inactivity
- Quality: losses due to defects
- Performance: speed losses
With GE Digital's Proficy OEE, various users will be able to create and view intuitive dashboards to monitor the efficiency of their machinery and lines, identifying the causes of production stops in an easy, fast and intuitive way. Obviously when it comes to OEE, some KPIs can only be standard, whatever the type of our company, and for this reason they are already included and set in the platform.
Among these we find some of the classic indicators, such as:
- MTTR (Mean Time To Repair): Indicates the average recovery time
- MTBF (Mean Time Between Failure): Indicates the mean time between failures
- MATR (Mean Amount To Repair): Indicates the average amount produced during a repair
- MABF (Mean Amount Between Failure): Indicates the average quantity produced between failures proficy OEE provides different KPIs but allows you to create your own indicators according to different needs. In order to analyze the data, it uses Proficy Historian as a database, but it can also use other systems, for example any relational database.
Gartner has recognized GE Digital as a leader in MES systems
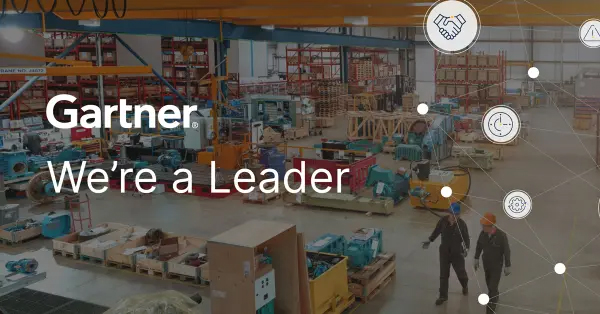
Gartner named GE Digital Leader in the 2023 Magic Quadrant for Manufacturing Execution Systems for its Proficy Smart Factory (MES) software solution. The evaluation was based on specific criteria that analyzed the overall completeness of the company's vision and ability to execute.
Also, find out Why Gartner Recognized GE Digital as Customers' Choice in Gartner® Peer Insights™ Voice of Customer 2023: Manufacturing Execution Systems.
Read your free reports today.
FEATURES
- Leverage critical KPIs to enable continuous improvement
- Make available standard reports, ad-hoc reports and dashboards for real-time decisions
- Synthesize and analyze data by context (e.g.: equipment, products, personnel, time (hour, shift, day)
- Automatically or manually associate events with causes and then analyze to identify root causes
- Scale your operational excellence solution
BENEFITS
- Boost the efficiency of assets and processes
- Reduction of equipment downtime and maintenance costs
- Better management of equipment life cycle
- Increased efficiency and productivity with improved visibility of operations and operator accountability
- Increase process productivity by identifying bottlenecks
- Increased quality ratio, reduction of waste