Bergkvist Siljan is a group that owns three sawmills in central Sweden. One of the sawmills is in Insjön, with 112 employees. The raw material is harvested from the surrounding forests.
In Insjön, the maintenance software Ides to plan, manage and track maintenance activities.
Johan Farth, technical resource at Insjön was interviewed together with his colleague and maintenance coordinator Joel Näs. Below their opinions and their experience with Idus.
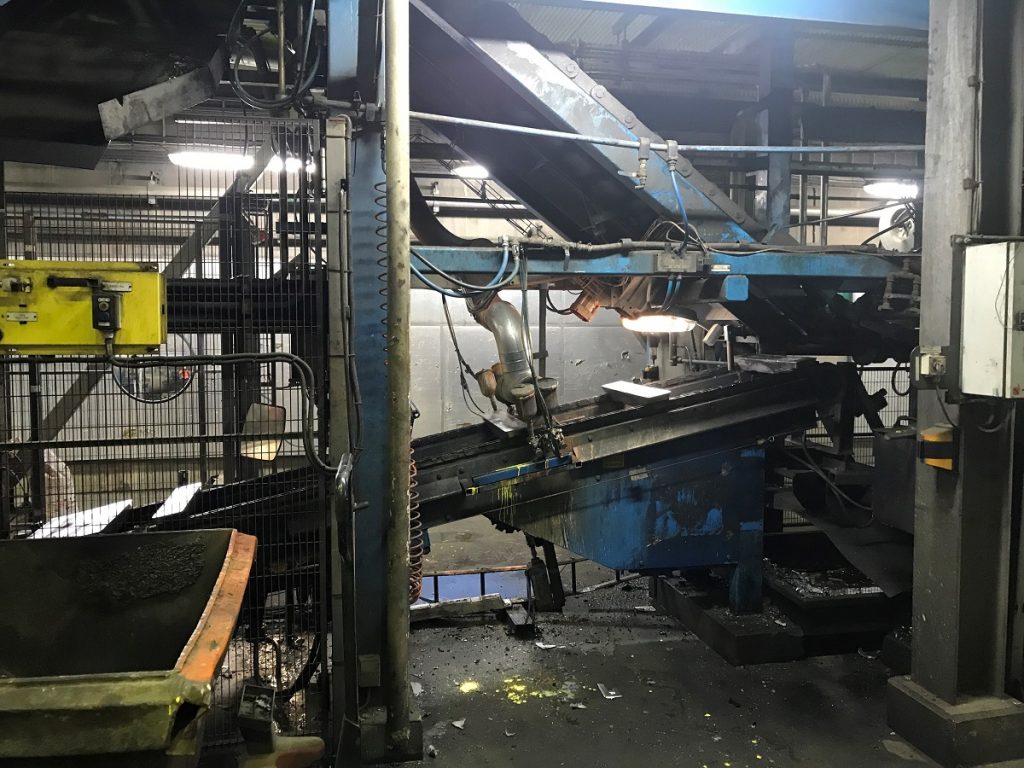
One of Sweden's largest sawmills
- We are one of Sweden's largest sawmills,” says Johan.
- Here we saw fir trees to pre-ordered sizes, mainly for building materials, most of which are exported to Asia. The sawmill has been in operation for almost 100 years.
- Production is active every day of the week, with maintenance stops during the night and on weekend evenings.
- We carry out maintenance 24 hours a day, all year round. We are about 24 maintenance craftsmen, from mechanics to electricians, up to the workshop and warehouse staff.
The goal is high availability
- We strive for a high level of availability, says Joel. We must ensure that the equipment is always in good condition to be operational. We frequently switch between dimensions and therefore it is essential to take the time to inspect and clean the machines.
- We clean the machines properly to avoid problems such as overheating and other functional losses and, at the same time, we carry out inspections to promptly identify other faults.
- This has positive consequences in several phases: we extend the life of the equipment, we do things at the right time, we shorten the time for maintenance interventions and we make sure that we have the right material at home at the right time”, says Joel.
Documentation and useful information - At Idus we have instructions on how to measure the wear of our machinery. It's important that everyone measures the same. We have well trained personnel who understand the importance of proper knowledge transfer.
- As far as planning is concerned, we want to know what repairs are needed, the level of wear and when the parts will be replaced, says Johan.
- We have good control of our backlog of work orders and can prioritize based on that backlog and the emergency jobs that arrive.”
Joel also points out the importance of documentation in the maintenance system.
- We have invested heavily in the documentation of the mill, so that useful information is always at hand. Electricians need to know many things in advance before starting to disassemble a machine: all this information is available in Idus, and they go through it together before starting.
- When it comes to corrective measures, it's easier in many ways to go back and open old work orders to see what we've done in the past,” says Joel.
- It is important information to collect in a memory bank and everyone in Insjön understands its importance. When we plan, it can be enough to check how the job went last time, checking the notes and the hours spent, to have a good indication for the next maintenance activity. Everyone understands the importance of collaboration and knowledge transfer, we have been using Idus for more than 20 years and it gives us a lot in return”, says Joel.
Effective corrective maintenance
- Machine operators go in and report faults, electrical ones go to the electrical department, and mechanical ones go to the mechanical department. Sometimes errors can be fixed quickly and then there is no planned outage, says Johan. In the case of major interventions, we do solid planning. We always have a number of interrupt jobs that we take the opportunity to do when we still have to stop the production line, so we take the opportunity to synchronize several jobs at the same time. We put work order numbers on the pallets and plastic containers to be prepared.
- Sometimes we get photos of various failures from production, it can be much easier to see how, for example, wear showed up on a conveyor when the belt was stopped, says Joel.
Quick snapshot - At Idus we have a dashboard that allows us to get a snapshot quickly, says Johan.
- It doesn't matter if you've been away or on vacation for 6 weeks, you can always see where we are with the goals, how things have been going lately and what the current trend is.
Idus dashboards provide a quick snapshot.
- When we talk, we can use Idus to understand the situation, the errors that have occurred and what we need to focus on, both in meetings and in informal conversations,” says Johan.
- We also have very good control of storage, Joel says. It's reassuring to know you have the parts in-house when delivery times for parts and materials are long.
- We have around 11.000 items and 650 picks a month, says Johan. All maintenance workers have the confidence that they can come in and pick material, they all understand the importance of documenting picks before things leave the warehouse. Overall, it can be said that we are in control of operations and that we have routines that everyone understands and is happy with.
Do you want to know more about Idus? Click below!