Con iFIX e WorkFlow Sirca aumenta qualità e sicurezza della produzione delle sue resine e pone le basi per il miglioramento continuo dei processi.
Dai serbatoi delle automobili agli chassis delle imbarcazioni, fino ai pavimenti in marmo artificiale: le resine poliestere insature sono un prodotto che trova largo impiego nel settore dei materiali compositi.
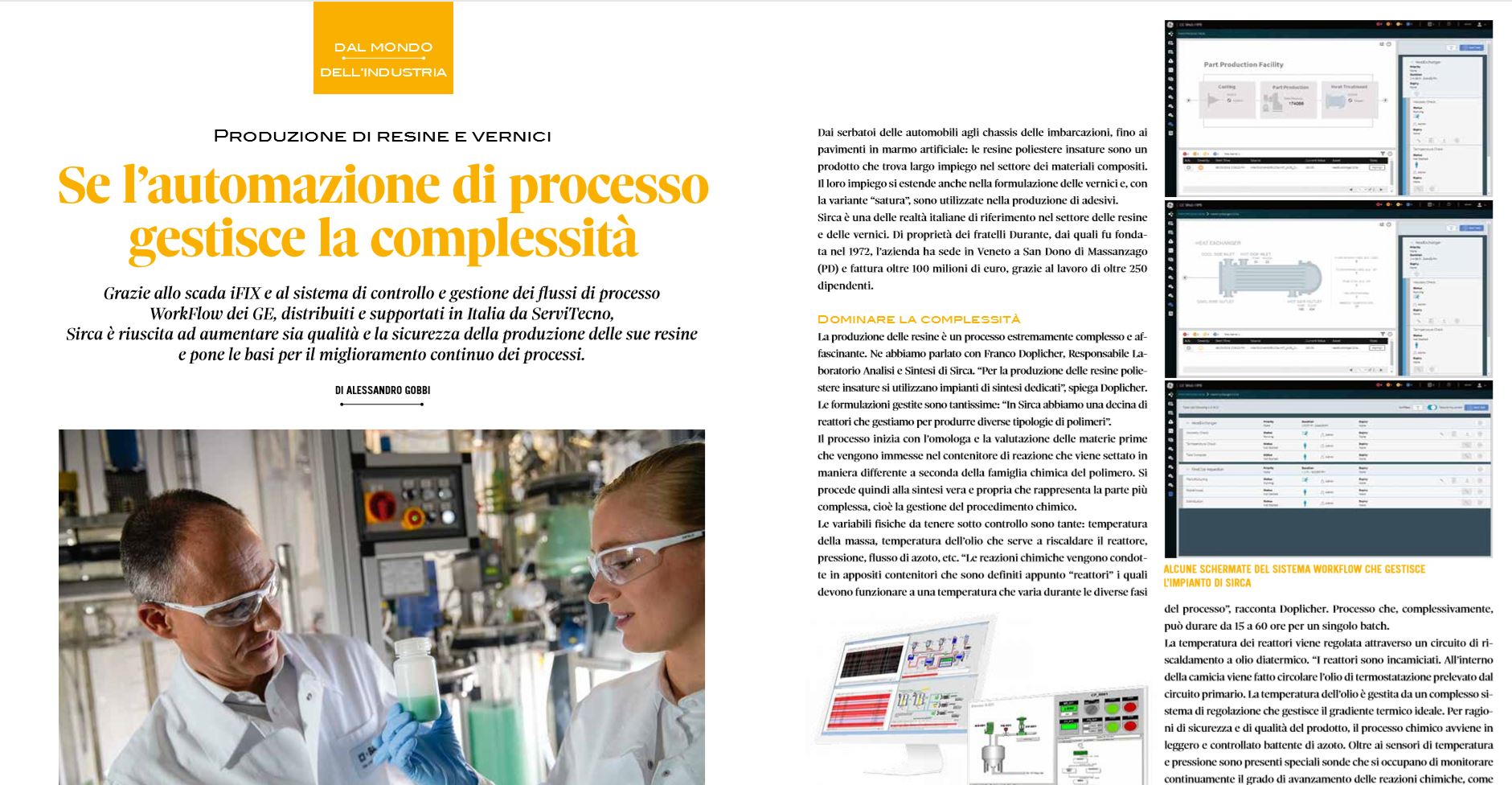
Case History Sirca – scarica l’articolo originale
Il loro impiego si estende anche nella formulazione delle vernici e, con la variante “satura”, sono utilizzate nella produzione di adesivi.
Sirca è una delle realtà italiane di riferimento nel settore delle resine e delle vernici. Di proprietà dei fratelli Durante, dai quali fu fondata nel 1972, l’azienda ha sede in Veneto a San Dono di Massanzago (PD) e fattura oltre 100 milioni di euro, grazie al lavoro di oltre 250 dipendenti.
Dominare la complessità

La produzione delle resine è un processo estremamente complesso e affascinante.
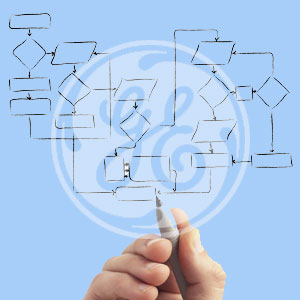
Ne abbiamo parlato con Franco Doplicher, Responsabile Laboratorio Analisi e Sintesi di Sirca.
“Per la produzione delle resine poliestere insature si utilizzano impianti di sintesi dedicati“, spiega Doplicher. Le formulazioni gestite sono tantissime: “In Sirca abbiamo una decina di reattori che gestiamo per produrre diverse tipologie di polimeri“.
Il processo inizia con l’omologa e la valutazione delle materie prime che vengono immesse nel contenitore di reazione che viene settato in maniera differente a seconda della famiglia chimica del polimero.
Si procede quindi alla sintesi vera e propria che rappresenta la parte più complessa, cioè la gestione del procedimento chimico.
Le variabili fisiche da tenere sotto controllo sono tante: temperatura della massa, temperatura dell’olio che serve a riscaldare il reattore, pressione, flusso di azoto, etc.
“Le reazioni chimiche vengono condotte in appositi contenitori che sono definiti appunto “reattori” i quali devono funzionare a una temperatura che varia durante le diverse fasi del processo“, racconta Doplicher.
Processo che, complessivamente, può durare da 15 a 60 ore per un singolo batch. La temperatura dei reattori viene regolata attraverso un circuito di riscaldamento a olio diatermico.
“I reattori sono incamiciati. All’interno della camicia viene fatto circolare l’olio di termostatazione prelevato dal circuito primario. La temperatura dell’olio è gestita da un complesso sistema di regolazione che gestisce il gradiente termico ideale. Per ragioni di sicurezza e di qualità del prodotto, il processo chimico avviene in leggero e controllato battente di azoto. Oltre ai sensori di temperatura e pressione sono presenti speciali sonde che si occupano di monitorare continuamente il grado di avanzamento delle reazioni chimiche, come ad esempio spettrofotometri e viscosimetri. Le variabili in gioco sono quindi diverse e i dati generati in un processo possono raggiungere una notevole complessità“.
Accedere ai dati per governare il processo
Anche se le normative del settore non impongono obblighi di tracciabilità, Sirca ha da tempo compreso l’importanza di avere sotto controllo i dati generati in ciascuna frazione di processo impiantistico: dalla gestione del circuito primario dell’olio a quella dell’olio in parete, dalla temperatura della massa in reazione fino alla pressione.
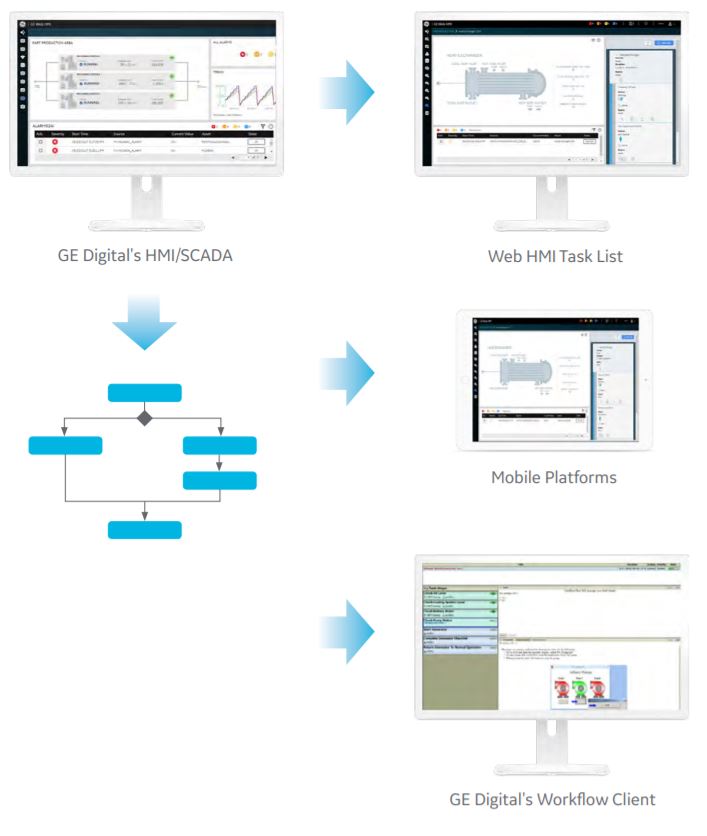
Dopo alcuni anni il sistema di monitoraggio e controllo della produzione impiegato da Sirca era diventato obsoleto rendendo eccessivamente lenta la consultazione dei dati di processo.“Questo – spiega Doplicher – richiede una registrazione dei dati che sia puntuale e veloce. La storicizzazione e l’analisi dei dati sono fondamentali per studiare, capire e migliorare le fasi del processo chimico così da ottenere un polimero con una qualità elevata e costante nel tempo garantendo nel contempo la sicurezza del processo chimico”.
E’ questo uno dei motivi che, qualche anno fa, ha spinto Sirca ad affidarsi allo scada di GE, iFIX, distribuito e supportato in Italia da ServiTecno.
Per l’implementazione Sirca si è affidata ad una primaria azienda operante in tutto il Veneto e all’estero.
L’automazione targata iFIX
“La nostra scelta è stata dettata soprattutto dalla necessità di disporre di un buon sistema di archiviazione. Per noi è cruciale avere i nostri dati sempre disponibili e accessibili con rapidità. In un batch, la cui lavorazione dura 60 ore, viene generato un notevole quantitativo di dati, sia per il numero di variabili controllate sia per la frequenza del campionamento“, racconta Doplicher.
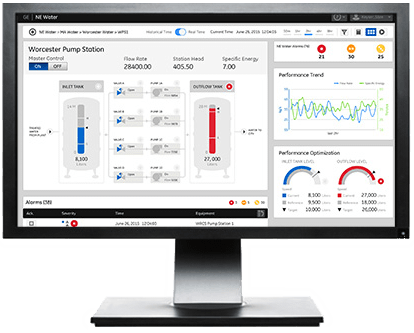
“Estrarre i dati su un momento qualsiasi del processo non è un’operazione semplice e iFIX ha dimostrato di saperlo fare bene“.
Anno dopo anno l’implementazione di iFIX è proseguita.
Oggi il sistema gestisce circa settemila variabili provenienti da una dozzina di PLC. “L’architettura della piattaforma prevede un server iFix, un terminal server per gestire i vari client, un server Historian e un server WorkFlow”, spiega il system integrator incaricato da Sirca.
Tutti questi server sono virtualizzati su una potente macchina fisica di cui si prende cura il reparto IT di Sirca. “Tramite il terminal server iFIX invia le informazioni a diversi client. Anche qui è stato però scelto di ottimizzare le risorse hardware”, sottolinea il tecnico. “Nell’area dei reattori, per esempio, ci sono due PC con 7 connessioni remote desktop associate ad altrettanti monitor.
Da ciascun monitor è possibile, con le dovute autorizzazioni, vedere le schermate di tutto l’impianto”. Il dominio di iFIX si estende poi anche al laboratorio, all’impianto di dosaggio dei catalizzatori e ad altre aree della produzione.
A occuparsi dell’immagazzinamento dei dati – la risorsa critica per Sirca – è il server Historian, che oggi gestisce tutte le variabili. Qual è il segreto della sua velocità?
“GE Historian utilizza una tecnica di compressione dei dati avanzata che consente di memorizzare una grande mole di dati senza occupare molto spazio o rallentare la macchina“, spiega il sistemista.
Dati che, inoltre, sono estremamente semplici da consultare: una apposita “vista” consente di accedere ai trend, che caricano i diversi gruppi di variabili.
L’operatore può muoversi nel tempo con grande semplicità per risalire allo stato delle variabili di un determinato momento storico. Infine, sono state predisposte delle query che consentono di esportare valori o tabelle in formato Excel.
WorkFlow, l’uomo in più del team
Lo scorso anno Sirca ha deciso di cambiare anche il sistema di controllo e gestione dei flussi di processo, scegliendo GE WorkFlow.
Si tratta di un sistema che ha un duplice compito: gestire direttamente e automaticamente alcune regolazioni ed elaborare i flussi di lavoro che saranno trasmessi al personale di campo.
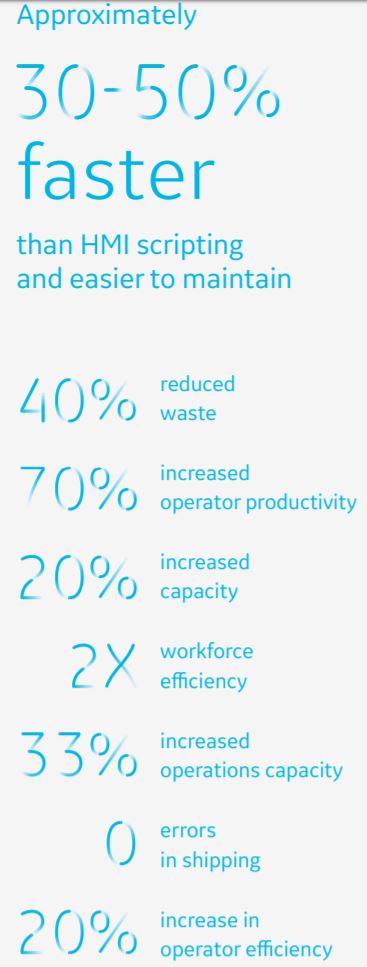
“Disporre di un tool che riesce a eseguire in maniera continua piccole regolazioni di processo consente di migliorare notevolmente la qualità del processo stesso. Prendiamo il caso della regolazione di un gradiente termico che, per esempio, deve aumentare di 40 gradi la temperatura del reattore in due ore. Un operatore regolerebbe la variabile in maniera discontinua con intervalli piuttosto ampi (25-30 minuti), mentre con WorkFlow l’operazione può avvenire con molti più interventi che garantiscono precisione e gradualità dell’incremento“, spiega Doplicher.
Ma WorkFlow è anche in grado di generare istruzioni visive per gli operatori in campo: da una serie di informazioni inserite in formato testuale vengono generati dei set di istruzioni sequenziali che dicono all’operatore fase per fase quali sono gli interventi da fare. “WorkFlow non ci sta soltanto permettendo di eliminare le istruzioni cartacee, ma è uno strumento di gran lunga migliore rispetto ad altre soluzioni elettroniche che però funzionano offline: i vantaggi di avere un sistema che ‘vive’ insieme al processo sono notevoli“.
Un altro vantaggio offerto da WorkFlow è la semplicità.
“WorkFlow offre un feeling ottimizzato per chi guarda il terminale. Ma GE non ha dimenticato anche il lavoro di chi mette a punto le procedure. Troppo spesso la creazione dei flussi di lavoro tramite programmi finiva per diventare un’attività lenta e penosa. WorkFlow invece è stato pensato anche tenendo presenti le esigenze dell’ingegnere di processo“.
“Per vincere la partita della competitività bisogna lavorare da squadra, dall’ingegnere di processo fino all’operaio che si occupa delle mansioni più manuali. La sensazione, però, è che con WorkFlow oggi il team possa contare su un uomo in più“.
WorkFlow si sta dimostrando migliore, più versatile e soprattutto meglio interconnesso del sistema precedentemente utilizzato.
“Quando si dà un’istruzione, per esempio, è possibile agganciare in parallelo altre istruzioni sempre scritte in WorkFlow. Questo è un fattore di grande importanza per chi gestisce processi complessi o più processi come nel nostro caso. Per esempio il software può occuparsi direttamente dell’incremento termico e parallelamente dare istruzioni all’operatore su un’altra zona di lavoro del reattore“. Con il passare dei mesi WorkFlow sta conquistando sempre di più la fiducia di Sirca.
“Recentemente abbiamo affidato a GE iFIX anche la gestione di una linea del reparto vernici. E, se le cose continuano ad andare bene, non è escluso che in futuro decidiamo di utilizzare WorkFlow anche lì“.