A molti sembrerà un paradosso, ma tra i tanti impatti avuti da questi lunghi mesi di pandemia, abbiamo anche visto un aumento della digitalizzazione dell’Italia che ha coinvolto anche le Aziende in molti settori, anche dell’Industria e delle Utility.
Non abbiamo assistito solo ad una miriade di call on-line e webinar: molti di noi hanno iniziato a capire che non siamo obbligati ad andare in ufficio e sul posto per “essere produttivi”. Abbiamo scoperto che molti lavori possiamo farli anche a distanza, “da remoto”, riuscendo anche a fare cose per le quali, fino a prima dei Lockdown, eravamo abituati a sorbirci chilometri e chilometri prendendo i mezzi più disparati, passando noiose ore e giorni per trasferimenti in auto, treni e aerei solo per fare interventi di pochi minuti o poche ore su macchinari ed impianti nelle fabbriche in giro per l’Italia.
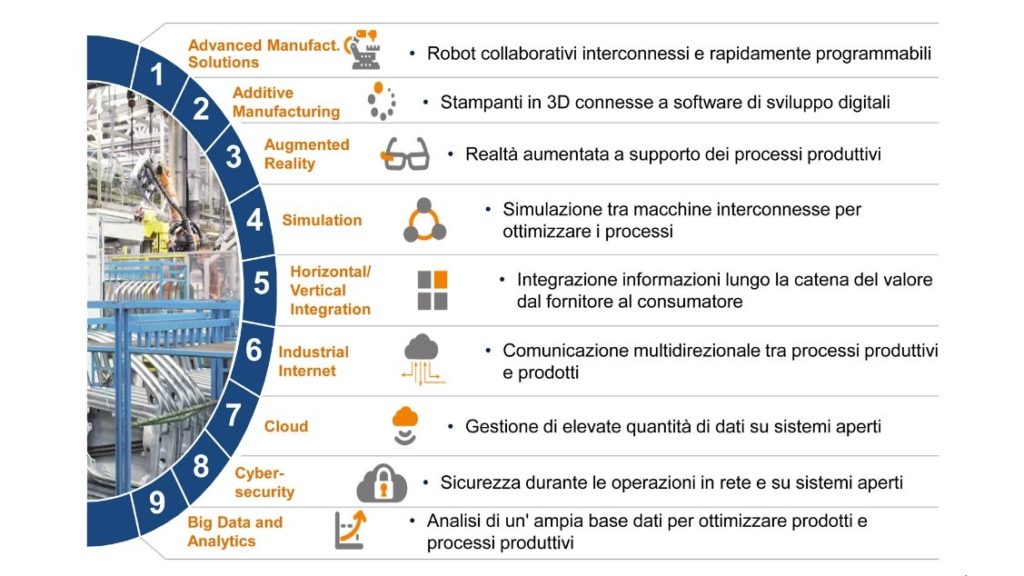
Già da qualche anno con i Piani Industria/Impresa/Trasformazione4.0 si sono gettate le basi per un impulso alla digitalizzazione degli impianti di produzione, nell’industria e nelle utility: si prevedevano estesa interconnessione, Industrial Internet, Integrazione IT/OT, utilizzo del Cloud, realtà aumentata, smart glasses anche in fabbrica…
…ma con scarsa convinzione, un po’ come mettere in vetrina un bel capo che però si sa che non si vende (o meglio non si usa).
Poi è arrivato il Covid-19, in un attimo quello che era solamente bello è diventato anche utile.
Si è capito che, data l’impossibilità di viaggiare ed andare di persona a fare interventi per la gestione e manutenzione del macchinario/impianto, era necessario accedere da remoto con funzionalità estese, come quando si è in loco: ecco allora la spinta per le applicazioni di Realtà Aumentata per interventi di manutenzione, la richiesta di ulteriori interconnessioni tra sistemi utilizzando tutte le reti di comunicazioni possibili, avere una replica delle videate SCADA dal tavolo in salotto o cucina di casa nostra, riprogrammare PLC e robot a chilometri di distanza, solo per citare alcuni dei casi che ci sono capitati negli ultimi due anni.
Ma anche le cose belle e utili, magari, rivelano dei risvolti pericolosi, basti pensare ai rischi associati alla esposizione in rete e l’allargamento del perimetro della rete di fabbrica da controllare e proteggere.
E qui vengono in soccorso ed entrano in campo gli specialisti di OT Cybersecurity, con dispositivi, tool e metodologie sempre più efficaci e semplici da installare e gestire: tutto al fine di ridurre al minimo impatti sulla continuità operativa, sulla produzione e possibili danni a persone, all’impianto ed anche all’ambiente.
Specialisti che riescono ad approcciare e mitigare i rischi legati alla “digitalizzazione forzata” attraverso metodologie che analizzano non soltanto gli aspetti tecnologici ma anche gestionali e organizzativi permettendo una più efficace assimilazione dei nuovi processi digitali.